ODrive Micro Datasheet
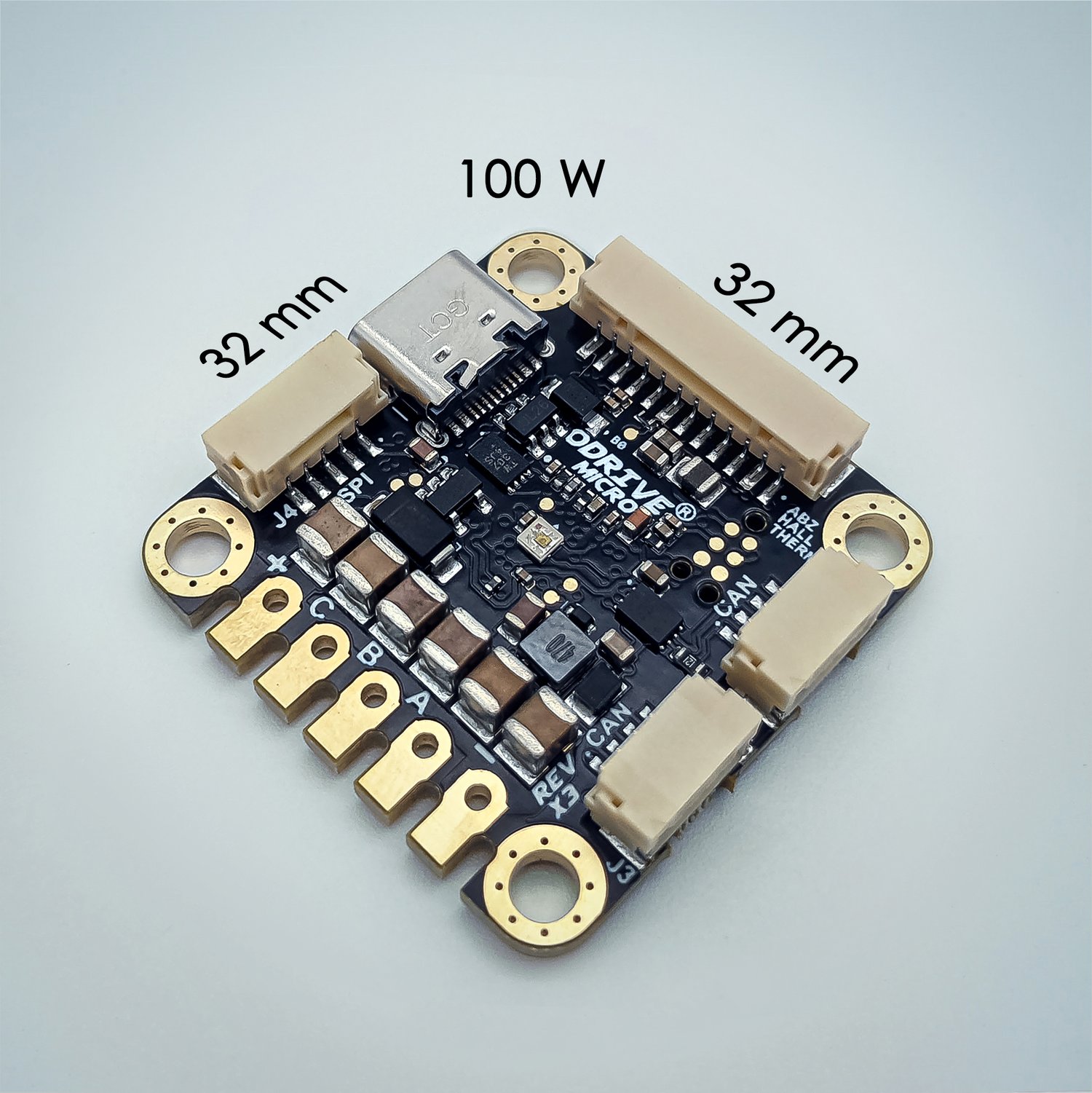
The ODrive Micro brings the high-performance motor control of the ODrive lineup to an ultra-miniature form factor, providing up to 100W continuous power in a tiny 32mm x 32mm footprint.
A CAN interface (hardware ready for CAN-FD, firmware planned) and an onboard 12-bit magnetic encoder allows for back-of-motor mounting, creating compact and high-precision actuators.
Electromechanical Specifications
Electrical
Note
All specifications are in 0◦C ≤ TA≤ 40◦C unless otherwise noted.
Specification |
Min. |
Typ. |
Max. |
Units |
Conditions and Notes |
---|---|---|---|---|---|
DC Voltage |
10 |
12-24 |
31 |
V |
|
Maximum Modulation Depth |
78% |
Utilizable percentage of DC bus voltage |
|||
Operating Motor Current |
3.5 7 |
A |
Free air (TA 25°C) Peak |
||
ESD Protection |
±30 ±13 ±8 ±16 |
kV |
Power Lines, IEC 61000-4-2 CAN Lines, IEC 61000-4-2 USB Lines, IEC 61000-4-2 All Other Lines, IEC 61000-4-2 |
||
CAN baudrate |
8 |
Mbit/s |
Additional firmware limitations apply, see |
Physical
Specification |
Value |
Units |
Notes |
---|---|---|---|
Mass |
11.7 8.1 6.8 |
g |
Euroblock Plug + Receptacle Euroblock Receptacle Bare Board |
Width Length Height |
32 32 7 |
mm |
|
Mounting |
PCB |
4x M3, 26mm x 26mm pattern |
Connectors
Connector mating receptacles and crimps.
Connector |
Description |
Connector P/N |
Mating Receptacle |
Mating Crimp |
Precrimped Wire P/N |
---|---|---|---|---|---|
Power |
Optional Screw Terminal |
OQ0532510000G |
TJ0531530000G |
N/A |
N/A |
J1 |
Motor/Encoder Feedback |
SM12B-GHS-TB |
GHR-12V-S |
SSHL-002T-P0.2 |
AGHGH28K305 |
J2,J3 |
CAN Connector |
SM04B-GHS-TB |
GHR-04V-S |
SSHL-002T-P0.2 |
AGHGH28K305 |
J4 |
SPI Connector |
SM05B-GHS-TB |
GHR-05V-S |
SSHL-002T-P0.2 |
AGHGH28K305 |
Environmental
Specification |
Value |
Notes |
---|---|---|
Humidity |
Non-Condensing |
|
Ingress Protection |
IP00 |
CAD
The ODrive Micro CAD model is available on the ODrive Micro OnShape page.
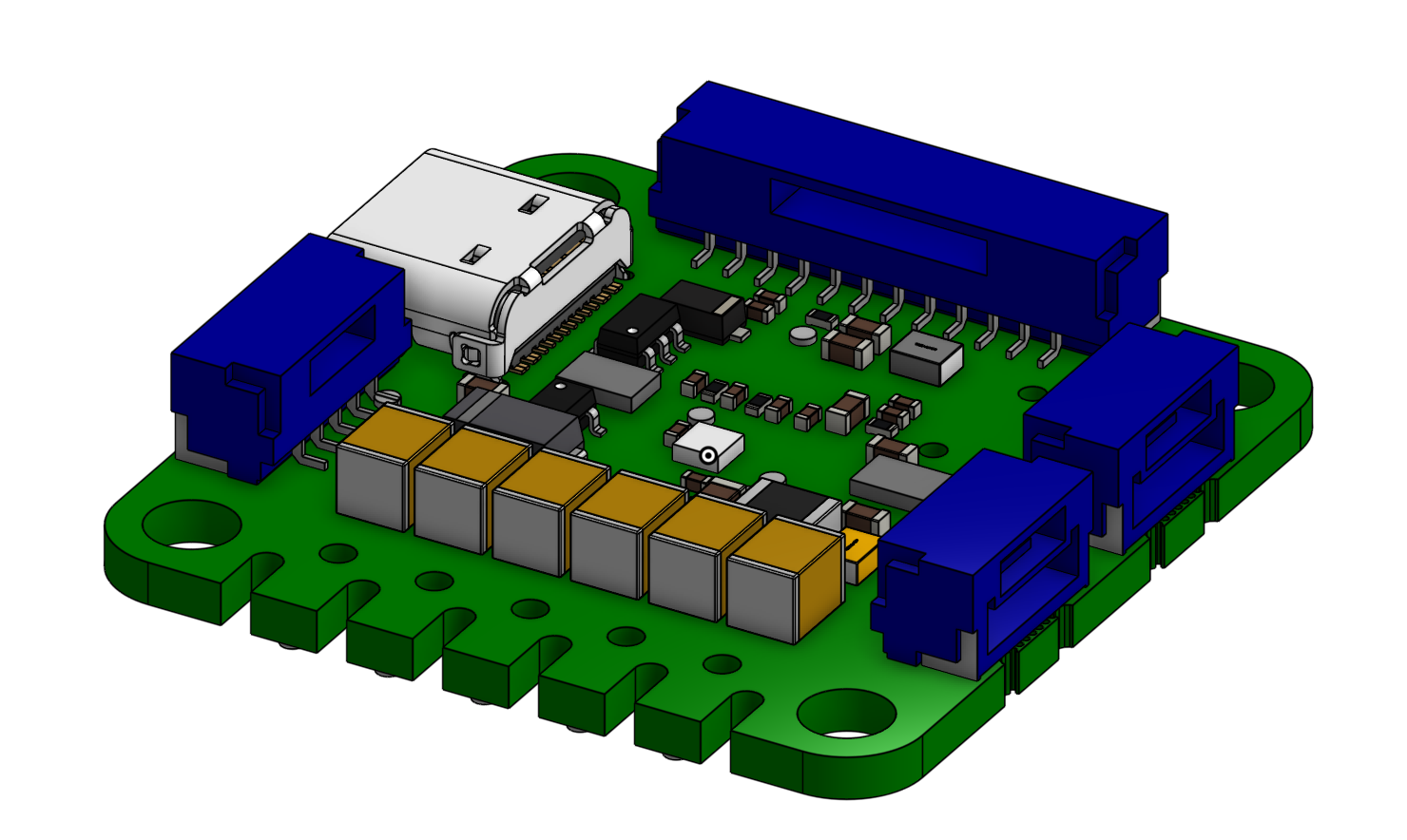
Pinout
Power Pads
Important
DC+- cannot tolerate reversed polarity, verify all power pad connections before energizing.
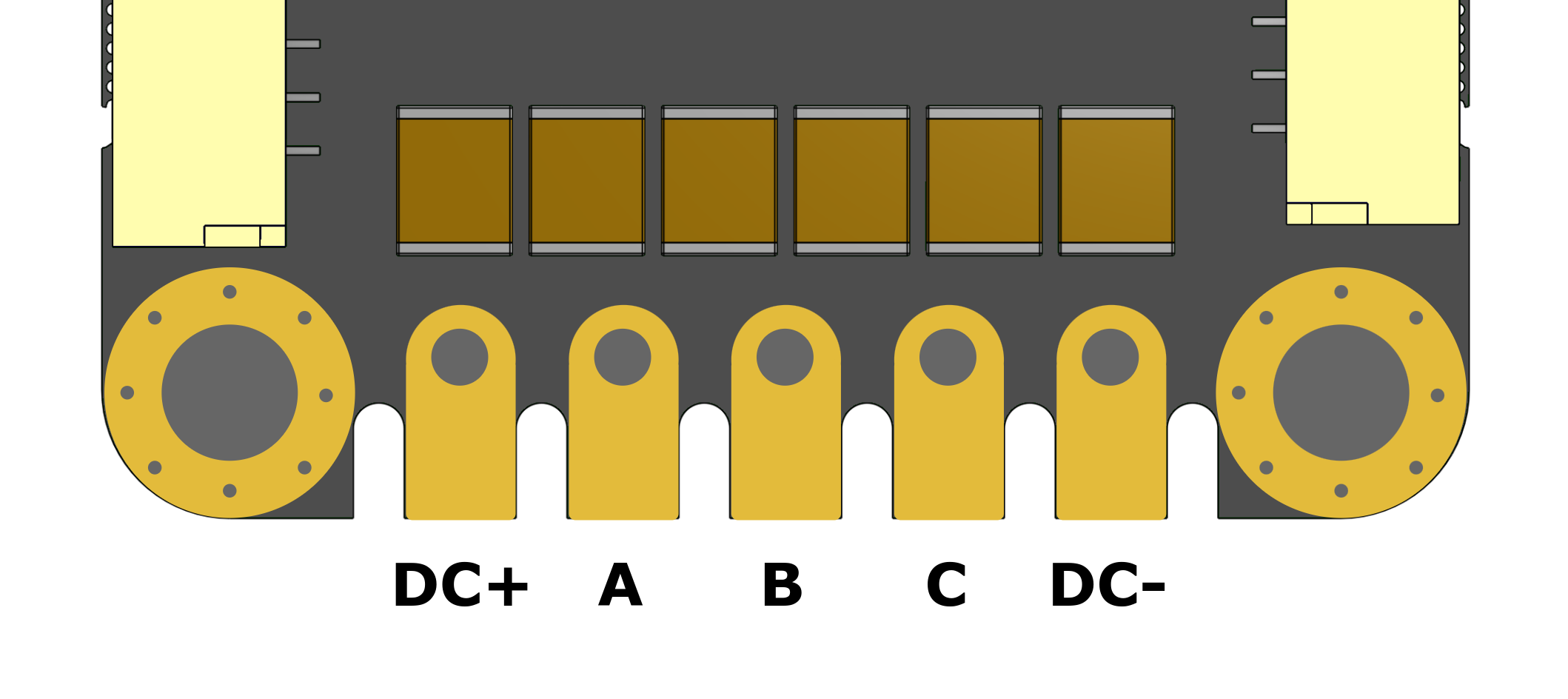
Pin |
Description |
---|---|
DC+ |
Power input, referenced to DC- |
A |
Motor phase A |
B |
Motor phase B |
C |
Motor phase C |
DC- |
Power ground |
The motor phase connections A/B/C can be connected in any order.
Logic Pins
All GPIO and SPI pins are 5V tolerant.
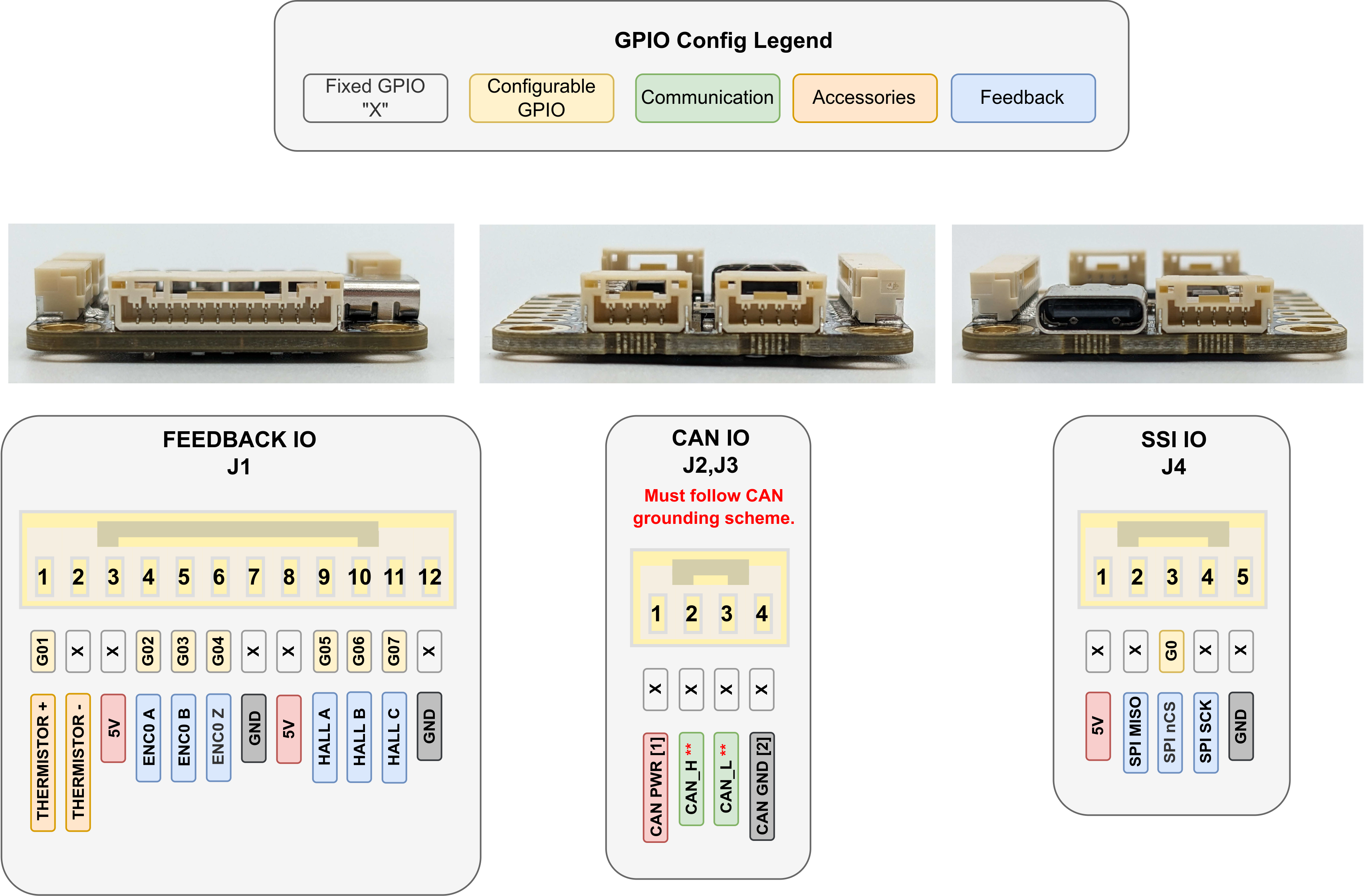
[1] CAN PWR is a passthrough and is not connected internally by default
[2] CAN GND is a passthrough and is not connected internally by default
See CAN guide for more information on proper CAN wiring and grounding
GPIO Properties
Additional notes and properties for each GPIO pin
G02, G03, G04: The ENC0 pins have a 2.7kΩ pullup to +5V, and cannot be used in DIGITAL_PULL_DOWN mode. When used as an output, the logic low level will be 500mV.
G05, G06, G07: The HALL pins have a 2.7kΩ pullup to +5V and low pass filter (τ=4.25us), and cannot be used in DIGITAL_PULL_DOWN mode. When used as an output, the logic low level will be 500mV.
G01: The THERMISTOR+ pin has an internal 1kΩ pullup to 3.3V for use in a thermistor sense circuit. It cannot be used in DIGITAL_PULL_DOWN mode.
G00: This pin can only be used as a SPI nCS pin, and should not be configured as a user-controlled input or output.
Notes
Note
The letter G and the zero padding are not used in odrivetool
or the web GUI, i.e. G09 would be represented by only the number 9.
5V outputs: combined draw max 100mA
The ODrive Micro does not have a dedicated SPI MOSI pin. The encoder SPI MOSI pin must be connected to either VCC or GND depending on the model:
AMS, CUI, RLS Orbis encoders: Connect MOSI to VCC.
MA702/MA732 Encoders: Connect MOSI to GND.
User Facing Pins (Gxx)
Locations for all pins that can be configured using
GpioMode
.- Inputs/Outputs:
G02-G07
CAN Termination and Power
By default, CAN PWR and CAN GND are passthroughs
CAN PWR and CAN GND can be connected to DC+/DC- by bridging the “J2/J3 ALT DC” solder jumpers on the bottom of the board. Note that DC+/DC- should not be connected at the same time as CAN PWR / CAN GND if this configuration is used.
A 120-ohm CAN termination resistor can be enabled by bridging the “CAN 120R” solder jumper on the bottom of the board
This allows for multiple daisy-chained ODrive Micros. Note that the internal CAN PWR / CAN GND passthrough is limited to 1A of current.